Our speciality is laser cutting, which allows us to achieve perfectly even edges while maintaining remarkable detail and repeatability of the obtained elements. We work on modern, high-quality equipment that comes from the factories of reputable manufacturers. Laser cuts are precise operations, which is why they are ideal for industries where it is important to process the metal to obtain the same product accurately.
We guarantee 100% repeatability. Such a high quality of work is possible thanks to the combination of modern machinery and effective technologies with a qualified team of professionals who have many years of practice and can boast of many professional and enthusiastically accepted projects. When ordering laser cutting services from our company, you can be sure that we will execute the order by the agreed date and that the effect will fully satisfy the customer.
What Laser metal processing service do we offer?
The catalogue of Elektron services is very extensive. We operate comprehensively, and thanks to this, we will find help for entrepreneurs operating in various industries. We use 2D (flat models) and 3D (three-dimensional models) processing technology. Our specialists offer, among others:
- sheet metal laser cutting,
- laser cutting of profiles,
- laser cutting of pipes,
Various patterns in metal, e.g., decorative elements, can be laser cut.
We work with various materials. We offer laser cutting services for carbon steel, stainless steel, aluminium, brass, and copper. We accept models of various thicknesses and shapes for processing. Our projects are not limited to objects with straight lines; we also undertake tasks related to irregular and unusual shapes.
CNC cutting-error-free, precise and fast
We are a true competitor in the market, delivering precision laser cutting services that provide our clients with components of identical dimensions and guaranteed repeatability. Our work achieves the highest accuracy thanks to a combination of team expertise and the use of the most advanced CNC laser cutting technology.
By leveraging modern laser cutting machinery, we ensure high-precision metal processing for steel, aluminum, brass, and other materials. The repeatable quality of our custom laser cutting solutions makes us a trusted partner in industrial laser cutting and fabrication projects.
It is an operation using numerical control technology. This means that the laser cutting of sheet metal and laser cutting of profiles or pipes is carried out with the help of a machine controlled by a special computer. It is therefore an automatic operation and not a manual one. CNC laser cutting of metal is not performed by a specialist – traditional hand-held devices are not used. This means that the work is free from so-called human error.
Manual metal processing involves a large margin of error. A delicate, even imperceptible at first glance, step beyond the template is enough, and the manufactured elements will differ. With manual techniques, there is practically no chance of maintaining repeatability. These are activities that are not applicable in industries where exceptional precision is essential. Therefore, if you want to obtain finished products, it is worth commissioning us to laser cut metal with the use of numerical control.
Contact Us for Customized Laser Cutting Solutions
Although CNC technology allows you to achieve the most precise results in your work, few people know what it is. The abbreviation comes from the English name “computerised numerical control,” which means computerised control of numerical devices. The machines used are equipped with a microcomputer, which is designed to manage and control their movements.
CNC metal processing consists of three stages:
- creating a computer project,
- its edition,
- making the element (excellent work).
In the first stage, special software is used that allows you to enter detailed data on dimensions, cutting angles, distances, edge thickness, etc. The goal is to create a project, i.e. a task for the machine. The entered command must be properly processed, for which the appropriate algorithm is responsible. The design is adapted to the capabilities of the machine tool and the nature of the material. The application includes, among others, factors such as surface roughness, local convexities, etc. The microprocessor edits the model data entered by the operator so that it corresponds to the real environment in which the machine will operate, allowing them to achieve the best effect.
The final step is to carry out the work through the device. All his movements are controlled by a computer. The metal laser cutting itself is done without human intervention. Its role is reduced to that of the operator. He is responsible only for entering data into the computer, i.e. programming the machine, and creating a command. Metal processing is performed automatically. That is why it is repetitive and error-free work, ensuring the highest possible quality.
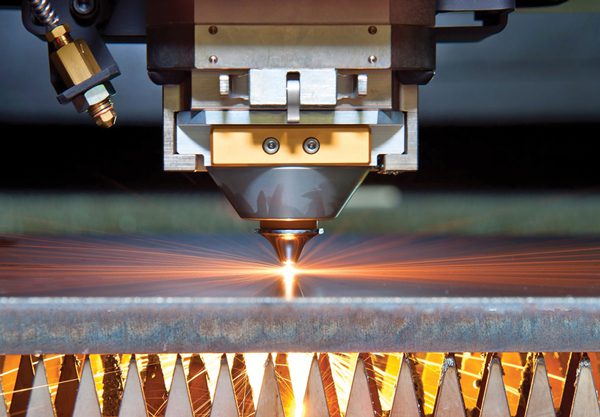
Advantages of our CNC laser cutting
The greatest benefits are, of course, the ability to maintain impressive precision, and thus obtain 100% repeatability when creating subsequent elements, i.e., obtaining the same ready-made items.
Another benefit is that it saves time. CNC laser cutting of sheet metal, profiles, pipes, or any other sort of metal processing is far faster than manual operations. Unlike humans, the machine does not become tired or require rest. However, the most important feature is that the data entered by the operator into the computer is saved, eliminating the need to manually program the device at successive laser activations.
such fast work allows us to significantly shortens the time needed to complete the order. Thanks to this, our clients can receive ready-made elements much faster than would be the case when working with traditional manual devices.
Ordering laser cutting appears to be a more expensive service on the surface, but it saves you money. What does it mean that this is possible? The machine’s flawless performance translates into the ability to make good use of virtually every received element, eliminating material losses, which is a common concern for clients ordering processing with hand tools.
With manual services, you will never achieve the same items, and in many industries, even minimal deviations render the model unusable and simply thrown away. CNC laser cutting is free from such hassles, which means losses, which usually involve the need to place another order to compensate for material shortages. Ultimately, the costs incurred are much higher than the cost of laser metal processing.
Laser cutting - principle of operation
A laser for cutting metal gives by far the best effect of any other technology. This technique produces the smoothest edges and, above all, is suitable for working with fine details and allows you to create any shape based on irregular lines. This is possible because the resulting cutting gap is only microscopically larger than the laser beam itself. This translates into a degree of precision so high that it is possible to create even complex geometric patterns.
Laser cutters are equipped with integrated diodes. They are responsible for producing the laser beam. Thanks to specially designed and extremely flexible optical fibres, it is then transported to the head, from which it is transferred to the material being processed. The stream drops to the surface, causing it to be heated until completely vaporized. Therefore, laser cutting uses the phenomenon of thermal separation. Its beam must penetrate the object as deeply as possible in a single location. When this happens, the actual cutting process begins, i.e., separating the material. It is happening at lightning speed.
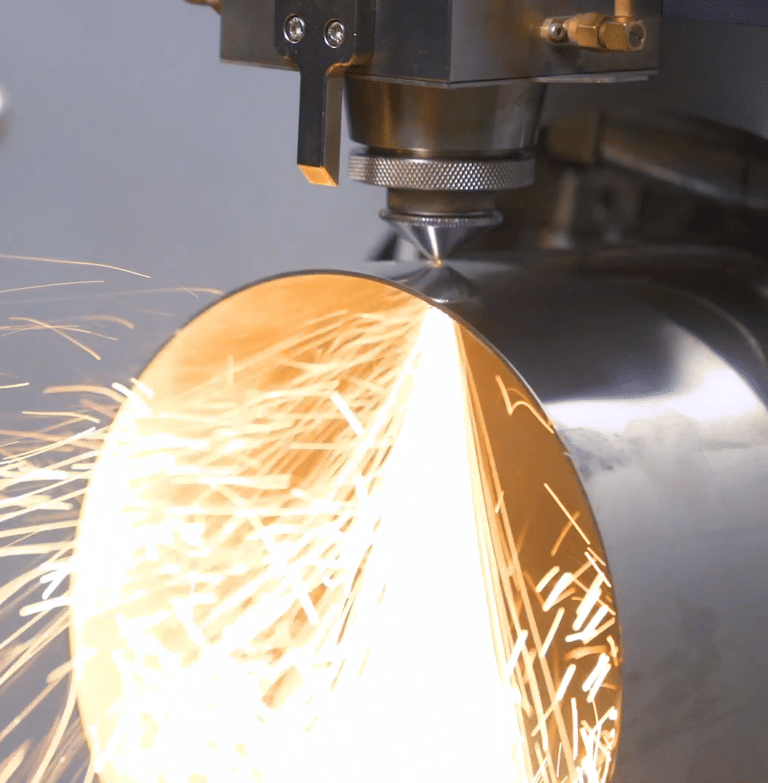
Laser cutting in metal - the advantages of using laser tools
The use of numerical control technology guarantees repeatability and error-free performance of the work. What are the advantages of laser metal cutting? It is a universal method, first of all. It can be used for machining various types of materials, e.g. steel, aluminum, brass, or copper. No other techniques are is widely used.
There are also no restrictions on the shape of the models to be worked on. Laser cutting can be performed on objects with straight lines as well as objects distinguished by irregular shapes.
The CNC allows you to shorten the time needed to complete the work. When this technology is used with laser cutters and not others, the job can be completed even faster. Laser processing of metals leaves perfectly smooth edges that do not require any finishing work such as grinding or polishing. When the component is removed from the machine, it is finished and ready for use. Thanks to this, the customer can pick up their order much faster.
How are we doing?
With each order that we accept from clients, we conduct a thorough interview with the client. Our ambition is to provide elements that will fully satisfy the expectations of our contractors, which is why we want to know their visions and needs. We also offer help and suggest the best solutions.
We always carry out the valuation individually to be able to offer the fairest possible offer. The price is adjusted to the scale of the difficulty, which determines the degree of involvement in the work. The lack of a fixed price is a plus because customers ordering simple actions do not overpay, as would be the case with the use of constant costs depending, for example, only on the number of workpieces.To obtain the highest quality and quick implementation, there is no need to look for advertisements such as “I will order laser cutting.” It’s best to contact us right away. We look forward to working with you!